Améliorations continues à la Combaude
Améliorations continues à la Combaude
En apparence, les procédés utilisés pour rechaper les pneus à chaud ont peu évolué au fil du temps. Mais en réalité, les progrès sont bien réels. Ils proviennent des connaissances acquises au fil des années par des opérateurs spécialisés. Ils se traduisent par des optimisations industrielles pour accroître la productivité et accompagner la qualité des pneus Remix rechapés. Michelin a accepté d’ouvrir les portes de son usine de la Combaude à Clermont-Ferrand dans le cadre de ce dossier. Visite guidée en compagnie de Jérémie Wojcik, responsable de la planification Remix.
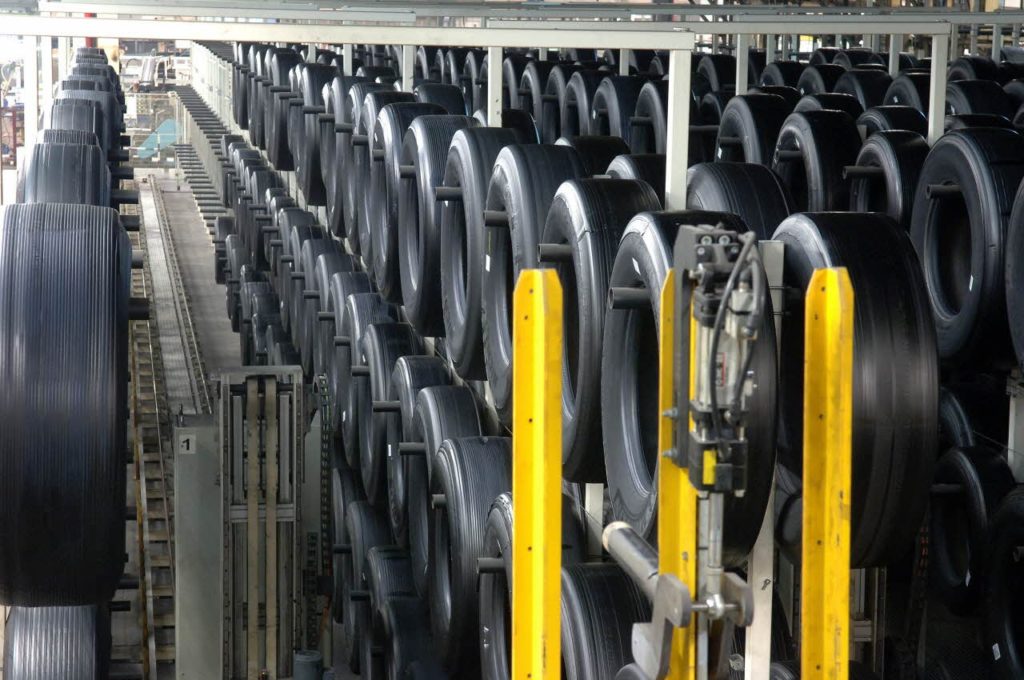
L’usine de la Combaude reste le vaisseau amiral de Michelin, avec une capacité de 500.000 enveloppes par an, du 215/75R17.5 au Maxi Trailer en 455/45R22.5. Le rechapage à chaud représente la plus grande partie de l’activité mais le site possède également un atelier de rechapage à froid, pour les petites séries (nouveau ou fin de produit). Les autres sites européens du Groupe sont calqués sur ce modèle, avec une offre Remix principale, mais aussi Recamic si besoin est, comme à Valladolid en Espagne, Alessandria en Italie, Homburg en Allemagne et Stock-on-Trent en Angleterre.
De la demande de collecte au pneu rechapé retourné, il s’écoule 42 jours en moyenne mais les pneus restent 10 jours seulement à l’usine. Sur le quai principal de l’usine, les camions viennent décharger les carcasses collectées auprès des négociants, qui sont ensuite regroupées par lots. Elles ont déjà été contrôlées au magasin central, qui reprend les bons de commande et se charge de saisir sur un système informatique toutes les caractéristiques des pneus (provenance, marque, modèle, dimension, matricule, etc.). Ces informations sont capitales pour Michelin qui entretient une base de données sur toutes les carcasses qu’il reçoit. Cette banque servira ensuite aux ingénieurs du centre de R&D de Ladoux, qui utiliseront ces données pour améliorer leurs nouveaux produits, ainsi qu’aux techniciens, qui devront prendre ou non la décision de rechaper une carcasse. Cette dernière tache est aussi la première qui intervient dans le processus rechapage. Une inspection visuelle est réalisée sur chaque pneu entrant pour identifier son origine, savoir s’il a déjà été recreusé et rechapé, noter son état général et souligner à la craie les blessures sur ses flancs, à l’intérieur et à l’extérieur de l’enveloppe. Sur le système informatique, toutes ces données viennent compléter la fiche de chaque carcasse. Ce travail minutieux s’effectue « à l’ancienne », dans une pièce sombre et avec une torche. L’opérateur la manie avec dextérité, effleurant de lumière la surface du pneumatique afin qu’elle révèle les irrégularités les plus subtiles. Entre 3 et 5 minutes sont nécessaires pour chaque pneu. Il en voit passer un peu plus d’une centaine par jour et peut décider de rejeter l’enveloppe. Certains dommages sont restrictifs, comme une altération du bourrelet. Parfois, c’est la combinaison de plusieurs blessures trop proches l’une de l’autre qui conduisent à créer un dommage restrictif. « Sur 100 carcasses, 10 ne passeront pas cette première étape », souligne Jérémie Wojcik.
Afin de détecter les défauts qui n’apparaissent pas à l’œil nu, les pneus sont auscultés par radiographie et shaerographie. Le premier examen révèle l'état des ceintures d'acier et des câbles dans la carcasse, ruptures éventuelles et abus de roulage à plat… Le second identifie et mesure les décollements de nappes éventuels en gonflant et dégonflant le pneu. Les pneus passent aussi à la gégène. Des courants électroniques puissants sont infligés à la carcasse pour déceler les moindres ruptures dans la ceinture radiale et les localiser.
A ce stade, tous les pneus ont chacun leur code barre, que les machines et les opérateurs scannent avant chaque opération pour assurer la traçabilité du produit. Des puces RFID vont se généraliser progressivement dans les nouvelles générations. Cette technologie a été lancée en janvier par Michelin sur les nouvelles gammes urbaines et l’usine de la Combaude se prépare à recevoir les carcasses d’ici 12 à 15 mois. Des gains de productivité significatifs sont attendus. Après avoir pris soin de séparer les commandes nominatives, qui sont prioritaires, les pneumatiques sont ensuite regroupés par lots homogènes de déformation. C’est la particularité du Remix Michelin. A l’usinage et à la cuisson, le processus de production prend en compte les caractéristiques propres à chaque carcasse et qui résultent de leur usage (aplatissement, agrandissement) ou de leur transformation (deuxième rechapage, amélioration des composants utilisés, etc.). Le goulot d’étranglement dans le processus industriel se situe en fin de chaîne, à la cuisson. Les choix dimensionnels des moules à utiliser pour la vulcanisation vont donc influencer directement les flux de production suivants. L’étape suivante est entièrement automatisée. A la Combaude, la cardeuse rechapeuse à commande numérique a juste besoin de lire le code barre du pneu pour effectuer ses taches : nettoyage du talon, polissage des nappes sommet et des flancs. La machine qui actionne le couteau, part du centre et creuse ensuite vers l’extérieur. Elle sait quelle courbe elle doit appliquer. En revanche, l’épaisseur de gomme à enlever varie en fonction du niveau d’usure du pneu. Michelin a donc mis au point un programme EGL (Epaisseur de gomme laissée), qui s’assure qu’une épaisseur minimum sera conservée, soit 0,5 mm de gomme. Cette performance est possible grâce aux informations collectées (génération de carcasse, matricule, déformation...), et garantit la qualité de l’habillage qui suivra. « C’est une différence avec le rechapage à froid, qui se contente d’enlever toujours la même épaisseur de gomme», remarque Jérémie Wojcik. Une carde vient ensuite préparer la surface pour l’étape suivante, en lui donnant un grain spécifique. Le cardage n’est pas uniforme. « Nous avons une courbe concave, qui prend en compte des mélanges spécifiques que nous souhaitons conserver pour nos carcasses ».
L’atelier pour les réparations contraste avec celui de la cardeuse, dont les robots sont protégés par une baie vitrée. Des opérateurs se partagent les taches. Le travail est pénible. Les défauts sont traités comme des caries. Il faut nettoyer l’infection, préparer la surface et « cimenter » le tout. Les progrès de Michelin sur ce poste concernent essentiellement l’ergonomie. Chaque position est étudiée pour réduire la fatigue. Les opérateurs portent des masques pour protéger leurs voies respiratoires des poudrettes. Les pneus sont dépoussiérés avant que l’opérateur applique un produit à bas de solvant à l’aide d’un pistolet, pour reboucher les perforations de la bande de roulement. A l’intérieur du pneu, un emplâtre est collé. Différentes qualités de gomme sont utilisées pour les flancs, le bourrelet ou la BDR. En moyenne, il faut 3 à 4 mm par pneu pour chaque poste de travail.
La reconstruction des nappes sommets et l’habillage sont des étapes à nouveau entièrement automatisées. La carcasse est d’abord pesée à nue, puis un robot vient appliquer une épaisseur de 1 mm de gomme de liaison sur toute la circonférence, extrudée dans une vis sans fin et posée via une tête de pose chauffante. C’est elle qui va garantir l’adhérence des nappes sommets. L’opération dure 2 à 3 minutes puis la carcasse est repesée pour s’assurer de la bonne quantité de gomme déposée. Elle est renouvelée sur les flancs de la même manière. Puis vient la bande de roulement, qui utilise les mêmes gommes que les pneus neufs. Toute la technicité de la machine réside dans le programme qui déplace la tête de pose et contrôle la quantité de matière déposée. « Sur un 22.5, nous rajoutons environ 19kg de gomme», précise Jérémie Wojcik, « l’objectif, c’est d’en mettre le moins possible, tout en garantissant la qualité du neuf ». Les nouvelles générations de gommes à faible résistance au roulement vont compliquer un temps le processus. Elles pourront être utilisées uniquement sur les carcasses X-Line ou de la génération SaverGreen.
La vulcanisation est la dernière étape de production. Auparavant, on a déposé une plaque en alu sur le flanc qui va marquer la gomme avec le matricule d’origine, essentiel pour la traçabilité. Le procédé est globalement le même que pour les pneus neufs. C’est vrai aussi au niveau de la durée de cuisson (50 à 60 minutes) et de la température (une centaine de degrés). En revanche, le moule va s’adapter aux nouvelles dimensions du pneu pour s’ajuster au plus près. Et comme la carcasse a déjà été cuite, seuls les flancs et la BDR doivent être vulcanisés. La presse utilise donc un autre mode de répartition de la chaleur. La vapeur est préférée pour les pneus rechapés, alors que les presses électriques sont devenues courantes pour les pneus neufs. Là aussi, des progrès ont été réalisés en 2009 à La Combaude pour adapter les moules à la génération des pneus Multiway. Leurs lamelles en forme de goutte d’eau ont posé des défis aux ingénieurs en ce qui concerne le déboitage. Une nouvelle ligne de presse a donc accompagné le lancement de ce produit.
En fin de chaîne, tous les pneus cuits sont inspectés visuellement. Ils sont également soumis à deux tests imparables. Chaque pneu doit subir une pression de 10 bars pour tester sa résistance et une décharge de 20 000 volts pour détecter toute perforation de la gomme intérieure, qui pourrait générer de l’oxydation. Enfin, un travail de finition manuel est réalisé avec une ébarbeuse pour gommer les défauts éventuels qui peuvent apparaître lors de la cuisson. Le pneu est enfin prêt pour retourner sur le marché. Il sera aussi performant que le neuf, insiste Michelin.