Très précieuses carcasses
En France l’année dernière, les ventes de rechapés ont même pour la première quasiment égalé celles de pneus neufs. Les économies générées par cette pratique ont du sens en temps de crise. Cette activité continue donc de progresser. Mais les carcasses ne peuvent pas toutes être rechapées et elles se font rares. Les grands manufacturiers « premium », qui dominent très largement ce marché, s’efforcent donc de sécuriser leurs flux. Les carcasses sont aussi l’objet d’une attention toute particulière depuis que la Commission Européenne s’interroge sur la meilleure façon d’appliquer son étiquette aux pneus rechapés, déjà en vigueur depuis le 1er novembre 2012 pour les pneus neufs.
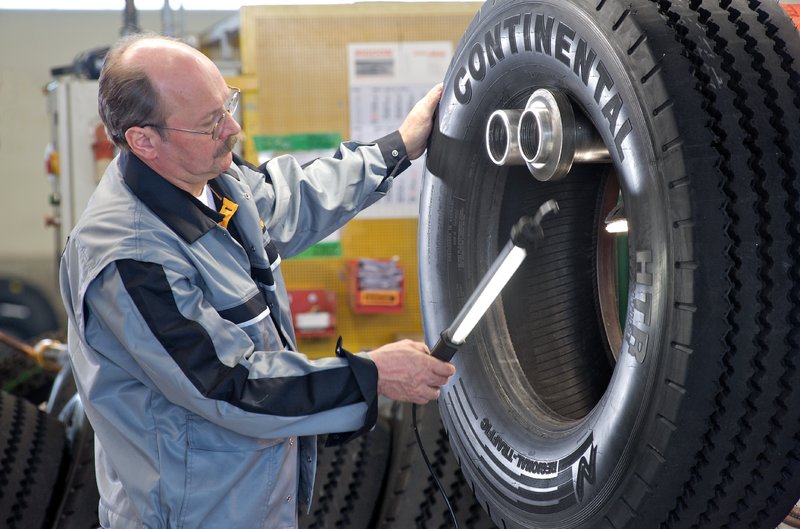
Le rechapage, une arme anti-crise ? La réponse est un oui, qu’il faut relativiser. Car sur le marché du remplacement des grands pays européens, le nombre de pneus rechapés vendus est aujourd’hui très proche du nombre de pneus neufs. Globalement dans l’UE, le rapport est de 40 pour 60, selon l’ETRMA. La part des pneus rechapés PL est la plus élevée en France (47 %), devant le Royaume-Uni (44%), la Scandinavie (42%), l’Allemagne/Autriche/Suisse (41%). Elle est la plus faible en Grèce (20%), dans les pays de centre et de l’Est de l’Europe (24%), l’Italie et le Benelux (28% chacun) et la Péninsule Ibérique (31%). En France, les transporteurs ont bien compris l’intérêt financier de faire recreuser puis rechaper leurs pneus, c’est-à-dire multiplier par 2,5 leur durée de vie en optimisant le potentiel de la carcasse.
Les économies peuvent aller jusqu’à 30%, par rapport à l’achat de pneus neufs et les prestataires promettent des performances quasiment équivalentes. De 30 à 50 jours, les délais peuvent être un peu longs entre la collecte et le retour en rechapé, mais les gestionnaires de flottes se sont organisés. Ils apprécient aussi de savoir qu’ils contribuent au bilan écologique des pneumatiques, en réutilisant leurs carcasses pour un premier, voire plusieurs rechapages quand c’est possible. Une autre preuve du niveau de maturité du marché est donnée par le poids très important du « nominatif ». En France, entre 75 et 80% des gestionnaires de flottes préfèrent rechaper leurs propres carcasses, qu’acheter des pneus rechapés. Ce taux est de 45% en Europe pour Michelin, mais leur nombre augmenterait au fil des années. La marge de progression en France, le plus grand marché d’Europe pour le rechapage, est donc considérablement réduite, à moins d’importer des carcasses de l’étranger.
Marges de progression
Au regard des statistiques de l’ETRMA, dont les membres totalisent 80% du marché des pneumatiques en Europe environ, l’activité rechapage en poids lourds gagne pourtant encore du terrain. En fait, les ventes en volumes baissent moins vite que celles de pneus neufs. En France, celles de pneus rechapés se sont inscrites en recul de 7,8% par rapport à 2011, alors que celles de pneus neufs ont chuté de 11,4%. La courbe des ventes de pneus rechapés suit celle des pneus neufs et se rejoignent progressivement autour de 880 000 unités.
Pour combien de temps encore ? En Europe, « la part des rechapés est passée de 37% en 2010 à 40% en 2012 », indique Fazilet Cinaralp, Secrétaire générale de l’ETRMA. Mais sur les 8 premiers mois de l’année, le recul est de 8% en volume par rapport à la même période en 2012, alors que les ventes de pneus neufs ont progressé de 5% sur les 6 premiers mois de 2013. Cette tendance devrait donc à nouveau s’inverser jusqu’en 2015-2016, le temps que ces pneus neufs arrivent sur le marché du rechapage. D’ailleurs, selon Fazilet Cinaralp, « les usines de rechapage des manufacturiers tourneraient actuellement à 75-80% de leurs capacités ».
En France, ce n’est d’ailleurs pas la priorité de Bridgestone. « Nous ne cherchons pas à recruter de nouveaux rechapeurs Bandag, car nous considérons que la couverture du territoire est suffisante », explique Michaël Codron, directeur de l’activité poids lourds de Bridgestone France et Benelux. « Par contre, notre objectif est d’augmenter les volumes de production de chaque atelier Bandag pour générer un certain nombre d’économies d’échelle et d’optimiser l’activité rechapage de nos partenaires ». Le groupe met ainsi à disposition l’ensemble de sa force de vente. Les équipes commerciales spécialisées dans les poids lourds ne font plus la distinction entre le neuf et le rechapé. Bridgestone porte aussi ses efforts sur le deuxième rechapage, « la seule manière pour le marché français de continuer à se développer », reconnait Michaël Codron. Continental est également offensif.
Jean-Michel Rouyer, Directeur de la branche Pneus Poids Lourds de ContinentalFrance revendique « 1 point de part de marché en plus en Europe de 2010 à 2012, et 3 points supplémentaires en France sur la même période ». Les raisons de ce développement relatif du rechapage sont structurelles. La crise a impacté le marché des véhicules industriels, en baisse de 8,9% en Europe l’année dernière (–9,2% en France), ainsi que le transport de marchandises depuis 2011, durement touchés par la hausse des carburants et des coûts d'exploitation. Les gestionnaires de flottes font rouler plus longtemps les pneumatiques de leurs véhicules pour retarder leur renouvellement et donc, leur rechapage.
Un constat partagé par Michelin, dans son usine dédiée au rechapage de ses pneus à La Combaude, près de Clermont-Ferrand. «Depuis 2 ans, les pneus qui nous reviennent sont de plus en plus âgés », remarque Jean-Luc Marchet, Directeur Marketing des activités rechapage de Michelin. « Soit les pneus sont mieux utilisés, car la technologie des pneus a progressé et leur longévité est améliorée, soit les camions roulent peu en raison de la situation économique ».
Sécuriser les flux de carcasses
Les 4 grands manufacturiers règnent pratiquement sans partage sur ce marché. Bridgestone revendique le rang de leader mondial et européen du rechapage après sa reprise de Bandag en 2007, et le lancement de son programme Total Tyre Life qui a suivi. Aux États-Unis par exemple, Bridgestone/Bandag (42%), Goodyear/Next Tread (28%) et Michelin/MRT (23%), contrôleraient à eux trois ce marché de près de 17,5 millions de pneus, selon les données 2011 du magazine Modern Tire Business. En Europe, Bridgestone, Michelin, Goodyear et Continental sont tout puissant, mais l’ETRMA ne communique pas sur les parts de marché. Celles des indépendants reste difficile à estimer, car les ateliers peuvent travailler sous contrat avec les manufacturiers. Mais elle se réduit sans doute, comme l’indique la reprise en main fin 2011 par Continental de ses activités rechapage, jusqu’alors confiées à l’indépendant Marangoni, et l’ouverture d'une nouvelle usine cet été à Stocken en Allemagne.
Ce revirement illustre l’intérêt stratégique pour les grands manufacturiers de maîtriser cette activité. Il annonce aussi par avance que les carcasses en circulation sur le marché seront encore plus convoitées. Sécuriser leurs flux faisait déjà partie des préoccupations des grands manufacturiers, qui ont implanté leurs usines et leurs ateliers de rechapage au plus près des grands marchés. C’est redevenu leur priorité. Leurs filiales et leurs réseaux sont sollicités. L’année dernière, Michelin a investi plus de 23 millions d’euros dans son usine de Campbell Road à Stoke-on-Trent en Angleterre, spécialisée dans le rechapage. Le manufacturier a modernisé les installations, de manière à gagner en productivité et intégrer les dernières évolutions technologiques. Avec sa filiale Pneu Laurent, il se partage les taches.
En France, Michelin prend en charge le 1er rechapage à chaud de ses pneus PL, laissant à sa filiale Pneu Laurent le soin de rechaper à chaud et à froid les pneus des concurrents, ou les siens pour un 2nd rechapage. Euromaster est mis à contribution pour la collecte des pneus à rechaper. Chez Bridgestone, on met l’accent sur le rechapage à froid, en s’appuyant sur le réseau Bandag, ainsi que sur First Stop et surtout les centres labellisés Truck Tyres.
Dans tous les cas, les réseaux après-vente des manufacturiers sont en première ligne pour organiser les collectes et s’assurer que les carcasses seront bien rechapées là où ils l’ont prévu. « Le fait de pouvoir profiter du gisement de nos carcasses donne de la latitude à nos partenaires rechapeurs », explique Michael Codron. Et de confirmer : « la collecte de carcasses et la maîtrise de carcasses nominatives est un sujet sur lequel travaille tous les manufacturiers ». Les actions commerciales auprès des transporteurs convergent vers ce même objectif.
Pour les grandes flottes, des contrats sont proposés au kilomètre parcouru, comme Michelin avec Norbert Dentressangle. Le manufacturier assure la gestion complète du poste pneu, recreusages et rechapages compris. Les pneus ne sont plus achetés mais loués. Cette prestation, « assez complexe à gérer », reconnait Jean-Luc Marchet, est prise en charge par Michelin Fleet Solutions pour des flottes d’au moins 200 cartes grises. Selon les pays, les manufacturiers peuvent proposer aussi à leurs clients de conserver leurs carcasses quelque temps, afin de les soulager d’un stockage éventuel, et de garder la main dessus…
Les ateliers sous la coupe du R109
Cette cohabitation des deux techniques de rechapage est une autre caractéristique de ce marché. La différence intervient en fin de chaîne, au moment de la dépose de la bande de roulement. A chaud, elle est vulcanisée dans un moule qui imprime les sculptures, alors qu’à froid, c’est une bande prémoulée qui est appliquée sur la carcasse avant la cuisson. Les opérations qui précèdent, inspection et réparation, sont similaires. Dans tous les cas, le processus de fabrication d’un pneu rechapé à chaud reste très différent de celui d’un pneu neuf. Il est gourmand en main d’œuvre et en capitaux.
Des réglementations existent qui encadrent le travail des ateliers de rechapage (UN-ECE R108 pour les pneus TC4 et R109 pour les pneus PL depuis septembre 2006). Elles s’assurent notamment que les rechapés ont des indices de charge et de vitesse équivalents à ceux des neufs qu’ils remplacent, qu’un système de suivi de la qualité est en place au niveau de la production et que les règles d’identification des pneumatiques sont respectées. En Europe selon Bridgestone, les deux techniques s’équilibrent pratiquement (52% à froid et 48% à chaud), mais de fortes disparités existent entre les pays. Le rechapage à chaud est incontournable en France (87%) et largement majoritaire au Royaume-Uni et en Espagne. Dans les pays scandinaves et ceux du centre et de l’est de l’Europe, le rechapage à froid est en revanche largement dominant.
En Allemagne, le rechapage à froid (65%) l’emporte également sur le rechapage à chaud (35%). Là encore, le rapport de force n’évolue pas vraiment au fil des années. En Europe, Bridgestone, qui revendique 25% de part de marché avec Bandag, voit pourtant le rechapage à froid gagner du terrain ces trois dernières années. En France, le rechapage à froid aurait même gagné 1,1 point de part de marché en 2012, par rapport à 2011. Mais à 12,8%, son niveau reste équivalent à celui enregistré en 2006. L’évolution reste donc très relative. Les investissements depuis 2011 de Goodyear Dunlop à Wittlich en Allemagne, de Michelin à Stock-on-Trent et la nouvelle usine de Continental, dont les volumes d’activités principaux restent en faveur du rechapage à chaud, lui donnent tort également.
Cet optimisme révèle d’avantage la volonté d’en découdre avec Michelin. « En France, nous estimons notre part de marché à environ 12%, contre 20% pour le neuf. Nous considérons donc le pneu rechapé comme la gamme où nous avons le plus de potentiel de développement », déclare Michaël Codron.
Bandag parie sur le rechapage à froid
Ce serait faire un raccourci de seulement invoquer des raisons historiques, qui signifierait que finalement, rechaper un pneu à chaud ou à froid reviendrait au même. C’est vrai en termes de marges entre un pneu neuf et un pneu rechapé pour les vendeurs. Mais le rechapage à chaud nécessite d’importants investissements puisqu’il faut un moule. Il convient donc mieux pour les carcasses de grandes séries. Le rechapage à froid est meilleur marché. L’outil est plus souple à mettre en œuvre et ce n’est généralement pas le manufacturier qui investit dans l’équipement, mais le licencié. Bridgestone en a fait sa spécialité aux côtés des indépendants. « Celui qui voudra ouvrir un centre Bandag, qui est un concept clé en main réunissant les équipements, la connaissance, les procédures, devra investir environ un million d’euros », indique Michaël Codron.
Le rechapage à froid permet donc de multiplier les ateliers pour mieux couvrir les territoires et d’optimiser la logistique client/usine. Ce qui explique pourquoi aux États-Unis, la grande majorité des pneus sont rechapés à froid (94%). Pour autant, les manufacturiers préfèrent garder la maîtrise des deux techniques, comme le prouve la nouvelle usine de Continental à Stocken. Mis à part pour Bridgestone, le rechapage à froid convient en particulier pour les petites séries, lorsqu’il est nécessaire d’être réactif vis à vis d’un nouveau pneu neuf concurrent, ou pour les fins de séries. Un pneu rechapé à chaud présente une qualité supérieure, à la fois en termes de performances et de finition, puisque les flancs sont refaits à neuf. Cet équilibre des avantages et des inconvénients empêche là encore toutes fortes variations dans les pratiques par pays.
Au royaume de Michelin et de Pneu Laurent
La France se caractérise non seulement par le taux le plus élevé d’Europe de pneus rechapés, qui en fait le plus grand marché d’Europe, mais aussi par un recours presque systématique au rechapage à chaud (près de 85% des volumes). « Et cela fait 60 ans que ça dure », selon Jean-Luc Marchet. Michelin et sa filiale Pneu Laurent dominent très largement ce marché aux dires des concurrents, mais les deux entreprises gardent leurs chiffres secrets.
Leur couverture des marchés sur le Vieux Continent est calquée sur la France. Michelin se charge essentiellement du premier rechapage à chaud de ses carcasses avec son offre Remix dans son usine de la Combaude sur la commune de Clermont-Ferrand, qui conserve une activité de rechapage à froid. Pneu Laurent, sa filiale basée à Avallon dans l’Yonne, gère principalement le rechapage des pneus concurrents en Remix et fabrique les bandes de roulement Recamic (rechapage à chaud et à froid) pour l’ensemble du Groupe. Elle est également capable de rechaper les pneus à froid.
Pneu Laurent emploie quelque 600 personnes, qui fabriquent chaque année plus de 1 million de produits rechapés en Poids Lourd, Génie Civil et de Bandes Prémoulées. Michelin ne communique pas non plus sur le chiffre d’affaires généré par les bandes Recamic, se contentant de préciser que l’activité Remix représente un plus gros volume et qu’il existe « une cinquantaine de licenciés en Europe, en incluant la Turquie », rapporte Jean-Luc Marchet. En Russie, une filiale du Groupe dispose de ses propres capacités de production sur un site qui est à la fois une usine et un atelier de rechapage à froid. Le procédé Recamic aurait été légèrement amélioré pour ce marché ».
La France est étrangement exclue de ce marché des bandes Recamic. « Nous n’en ressentons pas le besoin », se contente de répondre le manufacturier. Pourtant, juste à côté, en Italie, le marché est dominé en grande partie par des négociants rechapeurs, qui ont signé un contrat de licence avec le groupe Michelin, et qui ont le droit d’exploiter le procédé Recamic de rechapage à froid. Aux Etats-Unis, où le taux de rechapage est élevé, le Groupe se développe via une filiale MRT (Michelin Retread Technology), spécialisée dans les bandes prémoulées. « Les conditions d’usage, les charges à supporter et la typologie du réseau routier font que cette technologie est suffisante et ne pose pas de problèmes particuliers », déclare Jean-Luc Marchet.
En France, Michelin et Pneu Laurent à Avallon captent la grande majorité des carcasses qui circulent, mais d’autres ateliers existent bien. Bridgestone par exemple, dispose de 3 filiales : SLBR, qui a deux sites à Chaponost et Delme, ainsi les sociétés Rechapage du Centre (Moulins) et SOREVAL (Saumur). Le manufacturier travaille aussi avec les réseaux de Massa Pneus (Repneu Grasse), du groupe Simon (ABR à Quimper), d’Alençon Pneus (Renor à Bayeux), et Eco Plus Systems (Colmar). Seuls SLBR, ABR et Soreval pratiquent aussi le rechapage à chaud, et tous, le rechapage à froid. A Riom au nord de Clermont-Ferrand, Goodyear possède pour sa part une usine, qui rechape essentiellement les pneus à chaud.
Sans doute, tout nouvel entrant devra disposer de solides arguments s’il veut se faire une place. Les marchés étrangers semblent moins risqués. Après l’avoir testé avec le Grupo Soledad en Espagne, Hankook a lancé cette année en Angleterre sa ligne de pneus rechapés Alphatread. Elle comprend pour l’instant deux pneus directeurs en 295/80 R22.5 et 315/80 R22.5, ainsi qu’un pneu de remorque en 385/65 R22.5. L’anglais Bandvulc sera en charge du rechapage des carcasses de Hankook en pneus Alphatread. La France devrait suivre. Reste à trouver le bon partenaire.
Le rechapage : une solution écologique
Selon l’association européenne des fabricants de pneus rechapés, BIPAVER, réutiliser les carcasses plusieurs fois présente des avantages environnementaux pertinents. Environ 100 litres de pétrole brut et 69kg d’autres matériaux (caoutchoucs, silice, noir de carbone…) sont nécessaires pour produire un pneu poids lourds standard, alors que pour un pneu rechapé, 30 litres de pétrole et 15kg d’autres matériaux suffisent. Comme la production requiert moins d’énergie, les émissions de CO2 diminueraient également de 220kg à 39kg par pneumatique. Mais l’association ne prend pas en compte la variable logistique qui peut lourdement dégrader ce bilan, puisqu’il faut collecter le pneu, l’acheminer à l’usine, puis le retourner à son propriétaire.
Yann Le Chevalier, Directeur Marketing et Relation Clientèle de la division Pneus Poids Lourds de Continental France fait un autre calcul. Sur la base de 150 000 km parcourus, le coût d’un pneu neuf (315/80R22.5 en HSR, HDR et HTR 2ème génération) serait en moyenne de 3,24 centimes d’euros par km. Il passe à 2,90 centimes/km une fois rechapé à chaud en ContiRe et à 2,53 centimes/km une fois recreusé puis rechapé. « Cela représente 22% d’économie par rapport à un pneu neuf et 89% d’économie d’énergie sur le cycle de vie du pneu, en raison d’un besoin moindre de matières premières ».
L’offensive de Continental
Pour son grand retour dans le domaine du rechapage, le manufacturier a mis en place un cycle de production vertueux. Désormais, les gommes seront les mêmes pour les pneus neufs et les pneus rechapés. Elles intègreront toutes une proportion de caoutchouc, provenant de l’usine de recyclage. Les carcasses seront rechapés à chaud en ContiRe (44 dimensions pour le transport routier) ou à froid en ContiTread (6 dimensions. 6 dimensions avec la possibilité de 2 rechapages), non plus chez des partenaires, mais dans la nouvelle usine ContiLifeCycle de Stöcken, près de Hanovre en Allemagne.
Continental y a investi 10 millions d’euros et le site emploiera à terme une centaine de personnes. Sa capacité de production annuelle a été calibrée pour 180 000 pneus, dont 150 000 ContiRe et 30 000 ContiTread. Le groupe compte utiliser 4000 tonnes par an de matière recyclée (des carcasses non rechapables et autres PUNR, les poudrettes issues du cardage et des réparations avant rechapage). Selon Jean-Michel Rouyer, Directeur de la Division des Ventes poids-lourd, ContinentalFrance, « cela permettra d’économiser chaque année 2600 tonnes de caoutchouc, ainsi que 1400 tonnes de silice et de noir de carbone ». L’usine de Stocken démarre tout juste sa production. Le Pneumatique aura l’occasion d’en reparler dans une prochaine édition.
Bientôt du nouveau chez Bridgestone
Le manufacturier préparerait le lancement d’une nouvelle gamme de bandes prémoulées EcoTread, qui devrait cibler les carcasses de seconde ligne. Il a également annoncé l’arrivée au début de l’année d’une nouvelle technologie pour ses pneus poids lourds, baptisée Trisaver. Peu de détails ont filtré si ce n’est que le rechapage fait partie intégrante de sa conception et que la résistance au roulement sera abaissée. La date de commercialisation n’a pas encore été arrêtée.