Le futur de Michelin s’écrit à Cuneo
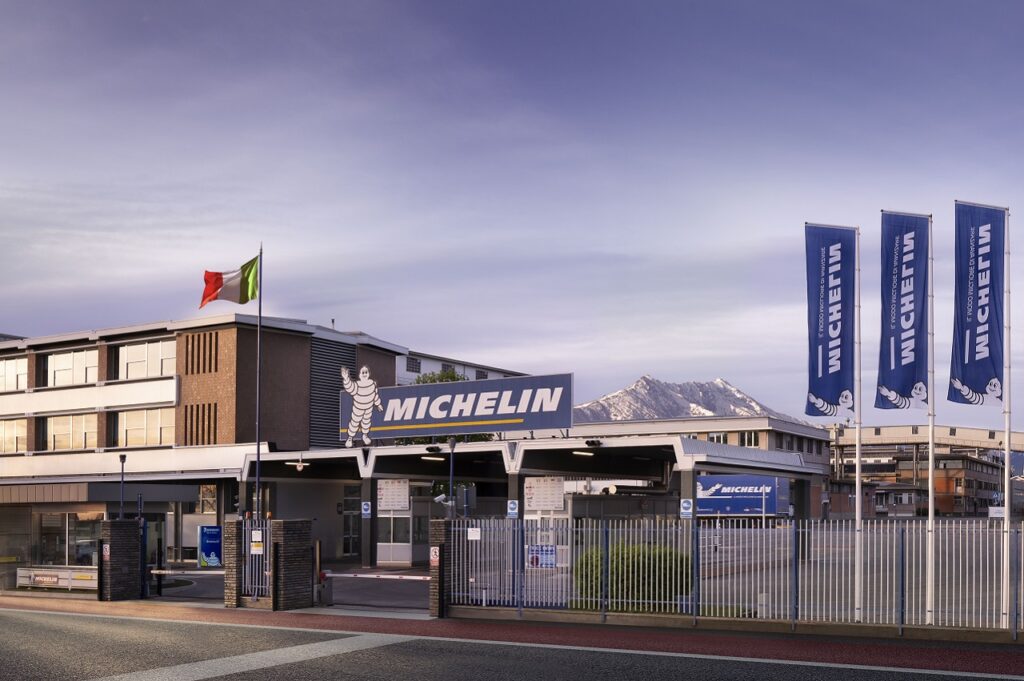
Le choix du site ne doit assurément rien au hasard, et nul doute que l’ouverture de ses portes ne dit pas tout de la réalité. Mais tout de même. Voir Michelin accueillir une trentaine de journalistes dans l’une de ses usines est un événement tout autant qu’une chance qu’il convient de saisir à sa juste valeur. De surcroît quand la visite se fait au sein d’une implantation en pleine transformation.
On a souvent mis en exergue cette industrie du pneumatique où cohabitent deux générations, avec des Européens et des Américains parfois plus que centenaires, traditionalistes, très reconnus, et de jeunes loups d’Asie (Chine, Corée du Sud…) plus flexibles, plus réactifs, capables de casser les codes et prêts à investir des sommes folles. À l’heure où une nouvelle page doit s’écrire, la remise en question demeure plus complexe pour les premiers que pour les seconds, étant acquis qu’il est plus difficile de transformer un modèle plutôt que de partir d’une feuille blanche.
Michelin a bien conscience de cela et travaille constamment à faire évoluer ses outils de production. En ouvrant les portes de Cuneo, le groupe clermontois n’entendait pas renier toutes ces problématiques qui collent à tous les "anciens" manufacturiers, mais davantage prouver qu’il est possible de les relever.
Une transformation qui ne date pas d’hier
L’histoire entre Michelin et l’Italie remonte au début du 20e siècle. C’est en effet par la Botte que Bibendum a amorcé son développement international, dès 1906, en ouvrant un premier bureau à Turin, là où se trouve encore aujourd’hui son siège italien. Au fil des années, d’autres bureaux mais aussi deux centres logistiques et trois usines vont voir le jour. Celle de Cuneo a ouvert ses portes en 1963.
Près de soixante ans plus tard, non loin des vignes de Barolo, un vin cher aux épicuriens, cette implantation est devenue l’une des plus importantes pour le groupe avec ses 925 000 m2, ses 2 200 employés et ses 13 millions de pneumatiques fabriqués chaque année. Spécialisé dans les enveloppes tourisme (15 à 21”), cet outil produit 74 % de ses volumes pour le marché du remplacement et 26 % pour l’équipement d’origine (Stellantis, BMW et Renault en tête), tandis que 80 % de ses pneus sont exportés dans toute l’Europe, dont 30 % dans l’Hexagone. Voilà pour les données préliminaires.
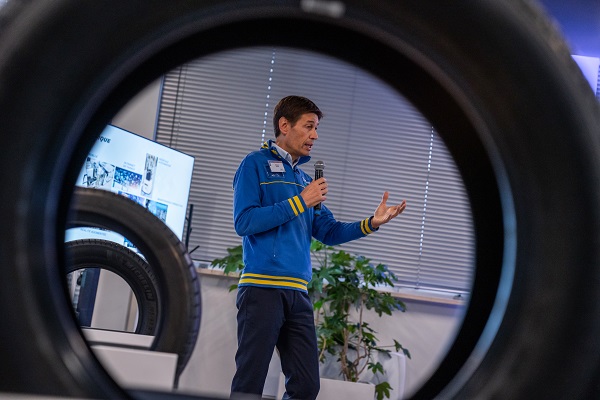
Sous la direction de Simone Rossi, l’usine piémontaise travaille main dans la main avec la R&D du groupe, basée à Clermont-Ferrand, pour développer certaines innovations telles que les puces RFID, les flancs velours ou le procédé Acoustique, diminuant l’impact sonore. ©Michelin
Ce qui rend Cuneo autrement plus intéressant est ailleurs. De l’extérieur, le site ressemble à bien d’autres manufactures avec des bâtiments grisonnants qui font leur âge. À l’intérieur, la donne est bien différente. Depuis 2005, Michelin s’est fixé une ambitieuse feuille de route pour transformer ses outils, tant d’un point de vue structurel que technologique.
Cette année-là est adopté l’i-MEP, un indicateur de performance interne mesurant la consommation d’énergie, les émissions de CO2, le prélèvement des eaux usées, la consommation de solvants, les déchets générés, etc. Une façon de se challenger pour devenir plus vertueux, comme l’a très justement précisé Jean-Christophe Guérin, directeur manufacturing.
Chaque détail compte
Une usine de pneus étant très énergivore, car on y transforme de la matière, et reconstruire ce type d’outil s’avérant très dispendieux, il a donc fallu faire du neuf avec du vieux. Au niveau des infrastructures, si cela ne saute pas aux yeux, les efforts se sont portés sur l’isolation, l’installation de pompes à chaleur, l’utilisation d’éclairages à LED, le déploiement pour les machines de nouveaux moteurs ou le recours plus important aux énergies vertes (22 % en 2021, avec l’objectif d’atteindre les 46 % en 2030 et 100 % en 2050). Entre parenthèses, le responsable note que "la crise actuelle est un accélérateur de sobriété énergétique".
Alors que la facture européenne de Michelin est passée en quelques mois de 300 millions à 1 milliard d’euros, ce contexte "pousse à aller toujours plus loin. Même une petite fuite d’eau doit être prise en compte et peut contribuer à améliorer notre performance écologique." Cuneo n’échappe pas à cet effort, qui se corrèle également avec ceux portant sur l’aspect fabrication.
Le site est en effet l’un des "leaders technologiques" du groupe, titre qui lui confère une place de choix dans le microcosme de Bibendum. Sous la houlette de Simone Rossi, aux manettes depuis un an, les équipes travaillent main dans la main avec la R&D basée à Clermont-Ferrand dans le développement de certaines innovations telles que les puces RFID, les flancs velours ou encore le procédé Acoustique, diminuant l’impact sonore.
La technologie au service des équipes
Étonnement, à l’heure de parler de tout ceci plus en détail, Simone Rossi commence par mettre en avant… l’aspect humain. "Une usine, c’est avant tout une aventure humaine, pose-t-il. Il faut emmener les équipes dans notre démarche, dans notre futur. On innove aussi pour eux, pour qu’ils se sentent bien ici et qu’ils soient fiers de venir travailler." Dans une région où le taux de chômage est quasi nul, Michelin joue localement un grand rôle sur le plan social avec moins de 1 % de turnover à Cuneo, une ancienneté moyenne de plus de vingt ans et des familles souvent représentées par plusieurs membres ou plusieurs générations.
Pour emmener tout le monde dans sa démarche, le groupe a d’ailleurs redéfini sa politique managériale en passant progressivement, depuis quinze ans, d’une logique d’équipes dirigées par un chef à une autre avec des équipes autonomes et des responsabilités réparties. Un modèle qui fonctionne partout. À Cuneo comme ailleurs, le groupe apporte les solutions et les employés se les approprient.
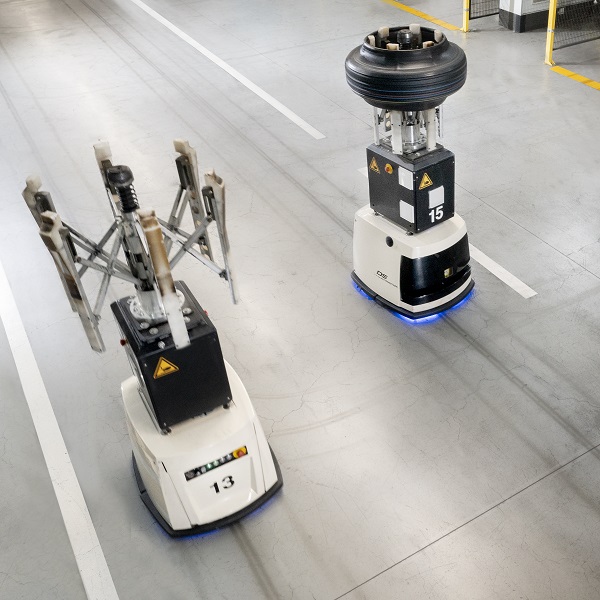
Aussi captivants qu’utiles, ces robots AGV animent l’atelier de cuisson en prenant en charge les pneumatiques pour aller les déposer dans les presses électriques, une autre prouesse technologique visible à Cuneo. ©Michelin
Pour en revenir à l’aspect purement technologique, la modernisation du site est une réalité bien visible. Au niveau de la confection de la carcasse, automatisation et flexibilité ont été érigées en maîtres mots. Entre le placement des tringles et la pose d’un code-barre d’identification, 3 minutes s’écoulent et 23 postes différents auront contribué à cette opération. Tous ne sont en revanche pas forcément utilisés. La pose des renforts sur les flancs n’est valable que pour les run flat, tout comme celle de la puce RFID, dédiée à certaines gammes. In fine, cette chaîne peut fabriquer entre 14 et 15 dimensions et/ou saisons simultanément.
Au niveau de la transformation finale, quand le pneu passe de l’état cru à l’état cuit, des efforts considérables ont été opérés par Michelin. L’atelier fait ainsi la part belle aux robots. Des bras articulés prennent l’enveloppe et la déposent sur des AGV, des petits robots mobiles circulant entre les différents postes et qui se chargent de récupérer le pneu puis de l’emmener vers l’une des presses de cuisson.
La révolution des presses de cuisson électriques
Après quinze ans de R&D, Michelin a enfin réussi à mettre au point un procédé de cuisson électrique. Encore une innovation maison. "C’est une technologie révolutionnaire, se félicite Jean-Christophe Guérin. La cuisson est une étape très énergivore. Nos presses électriques consomment 6 à 8 fois moins que des chaudières à gaz. C’est un gain spectaculaire." Encore fallait-il réussir à mettre au point le procédé pour éviter le fameux "pneu mollet", métaphore proposée à l’heure du dîner par Florent Menegaux, président du groupe, pour représenter une enveloppe ratée, car cuite à l’extérieur et crue à l’intérieur.
Aujourd’hui, la technologie est en place, bien au point et Michelin s’est donné un budget de 100 millions d’euros par an pour transformer progressivement son parc de presses. Une fois cuits (pendant environ 10 minutes pour ce type de produit), les pneus partent au refroidissement pendant une heure avant de passer à l’étape de la vérification. Une étape fondamentale pour un élément de sécurité pendant longtemps confiée uniquement à l’œil expert d’opérateurs, car le savoir-faire technologique n’était pas assez développé… jusqu’à Iris !
Le site de Cuneo profite en effet d’une machine révolutionnaire par laquelle passeront à terme une très grande majorité des volumes. Iris est ainsi dotée de 9 caméras 2D qui observent l’intérieur et l’extérieur du produit pendant 16 à 17 secondes. "Une vraie performance, car analyser du noir sur du noir est très complexe pour une machine", précise Cyrille Roget, directeur de la communication scientifique et innovations. Le dispositif, complété par des lasers, permet de déceler d’éventuels défauts. Toutefois, Iris analyse, mais ne décide pas. C’est uniquement l’opérateur qui décide si un pneu posant problème doit être retouché ou mis au rebut.
L’enjeu de l’impact sonore
Enfin, le site de Cuneo se veut également à la pointe en étant l’un des seuls chez Michelin à maîtriser la technique dite Acoustique. Avec le boom des véhicules électrifiés, l’impact sonore des voitures, avec une responsabilité substantielle imputée aux pneumatiques, devient un véritable enjeu. Après avoir développé cette activité façon start-up, l’usine piémontaise dote désormais près d’un million d’enveloppes de cette technologie composée de mousse en polyuréthane et de colle.
Un procédé rudimentaire, mais un savoir-faire quasi unique qui s’adresse aux VE mais aussi aux véhicules hautes performances. Toutes ces innovations font vivre la maxime chère à Michelin, "rendre possible ce qui paraît impossible" et surtout, elles posent les bases de l’industrie 4.0.
Ailleurs qu’à Cuneo, d’autres initiatives ont vu le jour, comme à Clermont-Ferrand où 4 000 logements sont chauffés par l’énergie produite par les installations du manufacturier, elles-mêmes raccordées au réseau public; comme dans l’usine des Gravanches, première au monde à zéro émission de CO2, ou encore comme dans l’usine d’Alessandria, non loin de Cuneo, qui bénéficie de la machine Osiris, automatisant la fabrication si complexe de pneus génie civil selon une logique similaire à celle d’une imprimante 3D. Plus que jamais, Michelin écrit le futur au présent et prouve qu’aucun outil industriel, aussi ancien soit-il, n’est impossible à réinventer.
Cet article est extrait du Journal du Pneumatique n°176-177 de novembre-décembre 2022.
Sur le même sujet
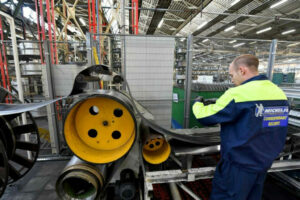