Rechapage : Continental ouvre les portes de sa nouvelle usine
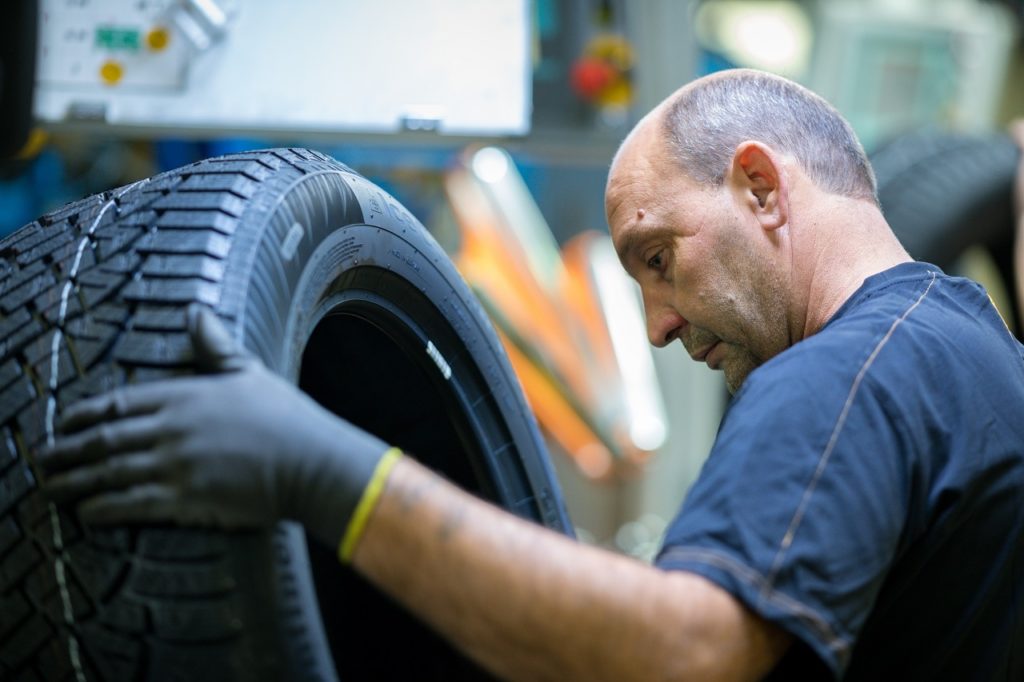
Dans son complexe industriel de Stöcken, près de Hanovre en Allemagne, le manufacturier a construit une unité de production spécialisée dans le rechapage. Opérationnelle depuis un peu plus d’un an, elle devient une brique essentielle de son offre ContiLifeCycle. Visite guidée.
Rares sont les unités de production à ouvrir en Europe de l’Ouest. Celle de Continental à Stöcken valait bien le détour. Elle est située dans son fief de Hanovre, plus précisément à 20 km au nord, sur un vaste site qui est dans le giron du Groupe depuis 1938. Un des bâtiments, qui accueillait une unité de production de pneus poids lourds a été entièrement rénové. Continental y a investi 10 millions d’euros et 16 mois ont suffi pour aménager le lieu, installer le parc de machines et tester les process. Tout se passe dans un seul et vaste atelier, repeint en blanc et baigné de lumière. Les flux entre les différents postes de travail ont été optimisés. Ils sont communs aux pneus qui seront rechapés à chaud et à froid jusqu’au cardage compris. Les deux techniques cohabitent à Stöcken, même si le rechapage à chaud reste l’activité principale. Car Continental a décidé de reprendre la main sur cette activité, qui était pendant un temps sous-traitée. Cette nouvelle stratégie a été mise en oeuvre en 2012. L’italien Marangoni se chargeait de rechaper ses pneus à froid depuis 2008 sous la marque Contitread, tandis que le rechapage à chaud était assuré par l’allemand Reifen Ihle avec ContiRe. Mais le manufacturier a finalement changé son fusil d’épaule il y a 3 ans.
Non sans raisons Il se vend en Europe et presque autant de pneus PL neufs que de pneus rechapés (936 800 pneus neufs et 828 700 pneus rechapés en France). Cette prestation est incontournable pour maintenir un lien fort avec ses clients Grands Comptes dans le temps. Et puis pourquoi laisser aux autres les bénéfices d’une carcasse de qualité premium, qui peut être réutilisée plusieurs fois ? Continental va donc devenir un acteur à part entière du rechapage en Europe. Des offres de services ont été développées autour du rechapage. « ContiLifeCycle » démarre dès l’achat d’un pneu neuf et s’achève avec le pneu rechapé, une ou plusieurs fois, selon ce que le client souhaite. « ContiCasingManagement » assure la gestion complète de la carcasse. Les plans produits aussi ont été révisés. Ainsi, pour la génération 3 des pneus PL, introduite en 2013, la gamme de rechapés est arrivée 6 mois seulement après leur lancement. L’unité de production de Stöcken redonne à Continental son indépendance industrielle. Le manufacturier a souhaité en faire une usine modèle. Elle prévoit même de recycler les déchets de pneumatiques dans de nouveaux mélanges de gomme. Sa capacité pourra atteindre 180 000 pneus par an. On n’y est pas encore. Les volumes de production de l’usine ont atteint 50 000 unités en 2013 et 80 000 en 2014. Ils doivent continuer d’augmenter progressivement. De nouvelles machines vont arriver dans le courant du premier trimestre 2015 pour accélérer la cadence.
A la shearographie d’abord
A l’heure actuelle, entre 2 et 5 camions viennent quotidiennement décharger leur précieuse cargaison. Elles arrivent de toute l’Europe. Celles qui ont été collectées sur le territoire français ont d’abord été centralisées dans un centre situé à Compiègne (Oise). Les carcasses les plus abîmées ont déjà été écartées après un contrôle visuel. Les autres reçoivent un code barre afin d’assurer leur traçabilité, avant d’être expédiées. Continental procède de la même façon au Royaume-Uni et en Italie, afin d’éviter des transports superflus. Le numéro 43 indique qu’elles proviennent de France. La première tâche des ouvriers qui les réceptionnent consiste à lire ce code barre, ainsi que le matricule du pneu, afin de rentrer ces informations dans le système informatique de l’usine. Pour celles qui n’en n’ont pas, on va leur en créer un. Puis les enveloppes les plus sales sont nettoyées. Les cailloux coincés dans les interstices de la bande de roulement sont extraits. Par ordre d’arrivée, elles vont ensuite subir un premier examen : une shearographie. Les carcasses sont alors déposées sur un convoyeur qui va les conduire dans un coffre à l’intérieur duquel on va créer un vide. Cette contrainte physique va permettre d’identifier les éventuels décollements de nappes, invisibles à l’oeil nu, via 16 photos réalisées sur toute la circonférence. Rares sont les pneus à avoir enduré de tels dommages.
Le taux de rejet à la shearographie se situe aux alentours de 5%. Cet examen est réalisé très en amont pour éviter que des carcasses en mauvais état encombre les flux. « Une deuxième machine va arriver dans le courant du premier trimestre », déclare Taha Ouadia, responsable de la production et guide d’un jour pour le groupe de journalistes français invités. Le classement dimensionnel des carcasses est effectué ensuite, et géré par informatique. C’est une étape essentielle, car il influence directement le plan de travail de l’usine. La production se cale en effet sur la disponibilité des moules utilisés pour le rechapage à chaud en fin de chaîne. Continental dispose ainsi d’un entrepôt où peuvent être stockées entre 16 000 et 18 000 carcasses dans des racks à 5 niveaux. Lorsque les ordres de production sont lancés, les carcasses subissent à nouveau une inspection, visuelle cette fois-ci. Trois postes sont dédiés à cette tâche, qui ont été fournis par Marangoni. Des opérateurs qualifiés examinent avec précision l’état du talon, repèrent les crevaisons, la présence de corrosion. Ils suivent une liste précise des contrôles à effectuer. Une lumière affleurante fait ressortir les imperfections. Les gestes sont rapides, précis. Les défauts identifiés à l’intérieur du pneu ou sur les flancs sont marqués à la craie, pour ceux qui seront en charge de les réparer. Ce travail nécessite de l’expérience. « Il faut environ 18 mois pour former une personne », convient Taha Ouadia. Un quatrième poste a été commandé, pour soutenir l’accroissement planifié de l’activité de l’usine.
Cardeuses numériques
L’étape suivante est celle du cardage. L’usine possède deux machines entièrement automatiques, que Continental a développé en interne. L’opération consiste à enlever la gomme de la bande de roulement. La cardeuse numérique va également râper les flancs des pneus qui sont destinées à un rechapage à chaud. Deux machines sont dédiées à cette opération d’une grande précision. Elles sont calées en fonction de la circonférence originale du pneu, qui peut varier avec l’usage. Elles prennent aussi en compte le volume de gomme à rajouter, s’arrêtant 1 à 2 mm avant d’atteindre la ceinture. L’angle de râpage est programmé, de façon à adopter une trajectoire concave ou convexe selon le type de pneu et leur dimension. Les poudrettes de gomme sont récupérées. Elles vont alors subir une série de traitements, afin d’obtenir un caoutchouc recyclé de qualité supérieure. Il peut être alors utilisé dans les mélanges de gomme utilisés dans les pneus neufs et rechapés. Plus légères, les carcasses devenues rugueuses sont aussi plus fragiles. Elles sont transportées par un système de convoyeurs jusqu’à un atelier de réparation. Quatre postes de travail sont prévus à cet effet. Les opérateurs disposent de toutes sortes d’outils pour « nettoyer les plaies ». On va traiter l’oxydation de la ceinture. On extrude de la gomme pour combler les perforations. Si nécessaire, des emplâtres sont collées sur la face intérieure. Parfois, les pneus ne sont pas réparables. C’est le cas lorsque le métal du talon est apparent, ou lorsque la ceinture est oxydée sur une zone supérieure à 8 mm.
« Le taux de rejet de l’usine avoisine les 15% », selon Taha Ouadia. Ce travail entièrement manuel nécessite le plus grand soin. A ce stade, les carcasses vont emprunter deux flux différents, selon si elles sont rechapées à chaud ou à froid. Ces deux techniques de production sont encadrées par le règlement ECE 109. Le rechapage à froid est assuré par une seule ligne de production. Elle comprend plusieurs étapes. La première consiste à appliquer une gomme de liaison sur le pourtour du pneu. Elle est déposée par une extrudeuse sur le sommet de la carcasse, en rotation sur un tambour. Son épaisseur peut varier de 0,5 à 2 mm. Une fois cette opération terminée, l’opérateur se saisit d’une bande de roulement déjà profilée et pré-vulcanisée, qui va être enroulée à son tour sur toute la circonférence. Ce protecteur de qualité d’origine est posé, en subissant une traction constante de manière à l’ajuster au plus près. Il est toujours fabriqué par Marangoni, selon les spécifications de Continental, tant pour le profil que pour le mélange de gomme. Pour la finition, une bandelette de gomme est appliquée à cheval sur les épaules et le flanc, entre la nappe sommet et la bande de roulement. Le pneu est introduit ensuite dans une enveloppe, à l’intérieur de laquelle on fait le vide. Reste alors à cuire le tout. L’usine dispose d’un autoclave, également fourni par Marangoni, pouvant contenir jusqu’à 20 pneus. Ils vont y rester pendant 3 heures environ à une température de 115°C, dans une atmosphère maintenue à une pression de 6 bars. « A la sortie, l’enveloppe doit être rapidement retirée, afin d’éviter qu’elle adhère au pneu, qui n’a plus qu’à refroidir à température ambiante », indique Taha Ouadia.
28 presses d’ici fin 2015
Le rechapage à chaud fait appel à un autre procédé, similaire à celui employé pour la fabrication de pneus neufs. Il consiste à déposer de la gomme brute au dessus d’une gomme de liaison. Une machine (en maintenance lors de la visite) se charge de cette opération. Elle est alimentée par des boudins de gomme ovoïdes, qui sont extrudés avant leur application sur toute la circonférence. Leur composition varie selon s’ils sont destinés à la bande de roulement ou aux flancs. En fonction de la dimension et du type de pneus, la machine est capable de calculer l’exacte quantité de gomme nécessaire, soit entre 18 et 22 kg de matière. Les pneus sont ensuite déposés sur un plateau et leur manipulation nécessite les plus grandes précautions. Ils sont alors prêts pour la cuisson. A Stöcken, Continental dispose aujourd’hui de 16 presses. Il y en aura 28 d’ici la fin 2015, répartie en 2 rangées de 14. Contrairement au rechapage à froid qui fait appel à des bandes pré-moulées et pré-vulcanisées, il faut « imprimer » le profil du pneu sur la bande de roulement, ainsi que toutes les informations des flancs. La carcasse est donc centrée sur un axe comportant une vessie gonflable et enserrée à l’intérieur d’un moule. Celui-ci est divisé en 10 segments pour faciliter le démoulage. Deux plateaux métalliques circulaires sont ajoutés pour marquer les flancs. Dans l’étuve utilisée pour la vulcanisation, les pneus vont cuire entre 45 et 50 minutes.
La vessie va appliquer une pression de 15 à 18 bars sur la face intérieure du pneu pour que la gomme prenne la forme du moule. La température atteint 150°C sur la bande de roulement et 130°C au niveau des flancs. C’est un peu moins que pour un pneu neuf, car il faut prendre en compte que la carcasse a déjà été vulcanisée. Le pneu est ensuite retiré de l’étuve et refroidi à température ambiante. Évidemment, Continental s’assure du bon niveau de qualité du produit fini. Il va d’abord être ébarbé pour lui redonner l’aspect d’un pneu neuf. On va aussi vérifier sa tenue à la pression en le gonflant à 8 bars. Enfin, un pneu rechapé sur dix va repasser à la shearographie. Au total, 3 heures sont nécessaires au processus de production des pneus rechapés à chaud. C’est une heure de moins en moyenne que pour les pneus rechapés à froid. L’efficacité de Continental pourrait être aisément qualifiée de germanique. « Les pneus restent en moyenne 72 heures dans l’enceinte de l’usine », assure Taha Ouadia. C’est peu, mais ce délais peut atteindre 15 jours à 3 semaines, si la commande est nominative et concerne une dimension peu courante. Continental est donc paré. Il faut maintenant que le marché suive.
En France, selon Continental, les ventes de pneus PL neufs ont augmenté de 9,9% et celles de pneus rechapés de 2,1% seulement. Véronique Giraud, Responsable de la division PL de Continental France, est plutôt pessimiste pour cette année, tablant sur un recul global de 2% sur un an. « L’activité devrait renouer avec la croissance en 2016, si la réglementation sur le transport de voyageurs s’assouplit ». Cela devrait être effectivement le cas au regard de la loi Macron, qui prévoit de libéraliser les lignes d’autocars sur tout le territoire national.
Sur le même sujet
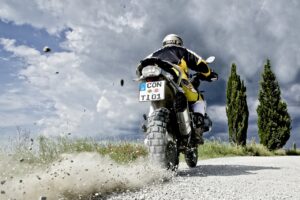