Thule Easy-fit Chaîner une roue en 12 secondes !
Qu’importe si cette année l’hiver n’est pas encore au rendez-vous, rien n’est perdu car d’abondantes chûtes de neige peuvent encore survenir. C’est ce qu’on espère dans la Profession et chez Thule, n°1 des ventes de chaînes en France et incontestable leader technologique avec sa chaîne VP Easy-fit, qui se monte en 12 secondes. Prix de l’innovation à Equip Auto, Livre Guiness des records avec 82 chaînes montées en une seule minute par 12 personnes, Easy-fit surfe sur les récompenses, elle a carbonisé le cauchemar du montage de la chaîne. L’occasion pour Thule Group de faire visiter son usine de Molteno, près de Milan, qui fabrique les chaînes Thule et König, et publier d’intéressants tests du TÜV comparant les performances de tous les dispositifs hivernaux, neufs et usagés. Avec, devinez-quoi, le chaînage en grand vainqueur,...
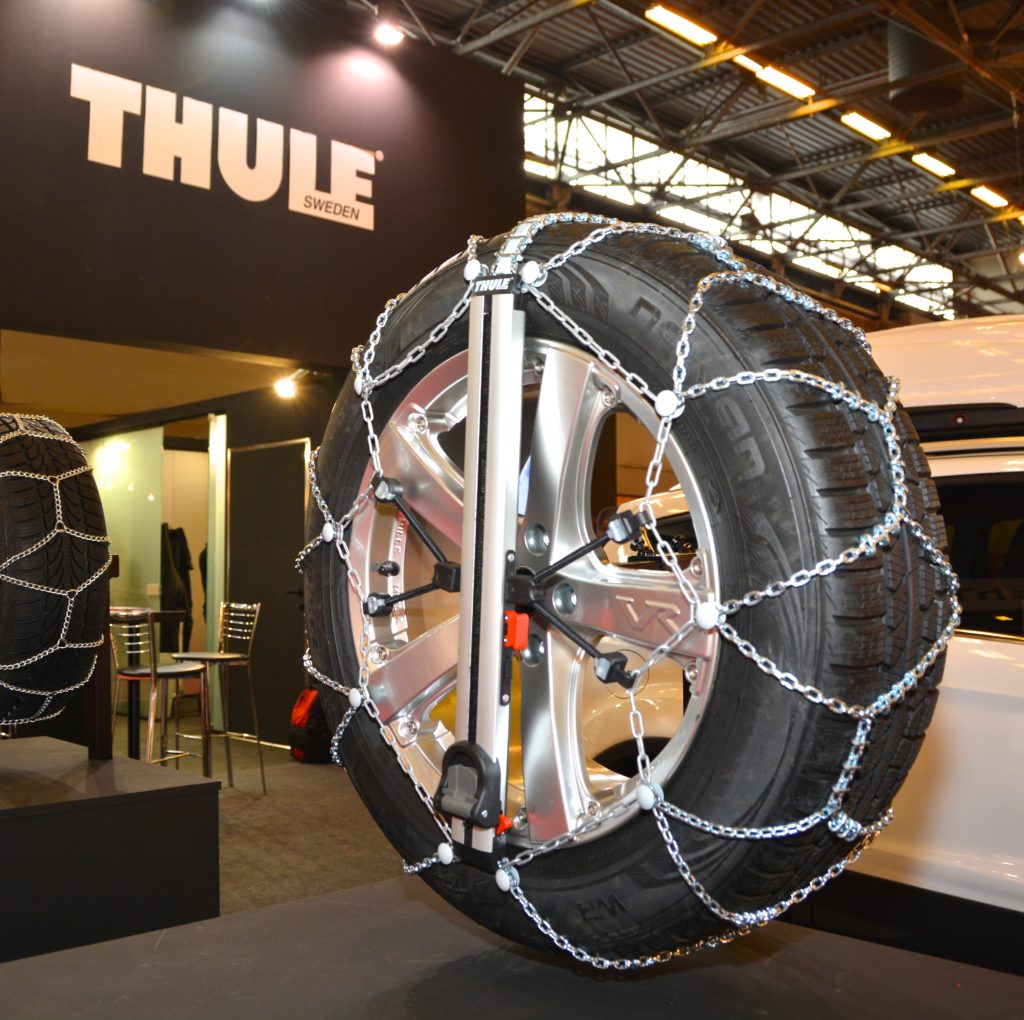
Réservé aux zones montagneuses et tempérées-froides de la planète, l’usage de la chaîne à neige ne connaît pas de déclin. Les progrès certains des pneus hiver n’ont rien changé, ils n’empêchent pas, lorsque les conditions deviennent difficiles, le recours obligatoire aux chaînes. Unique dispositif 100 % efface sur tous les sols, sa meilleure justification est qu’il chausse les engins de déneigement (et les engins forestiers travaillant en terrain meuble). Son seul défaut réside dans sa vitesse limitée sur le sec, mais au delà de la technique la difficulté de montage/démontage reste le frein majeur à son utilisation par les automobilistes, étant donné que les professionnels sont moins touchés puisqu’ils montent souvent les chaînes fin automne pour les retirer au printemps. D’où la très logique politique produit du Thule Group (prononcez Toulé) qui vend au particuliers des chaînes à montage rapide Thule et aux professionnels des dispositifs plus simples et résistants sous la marque König.
Groupe international
Surtout connu pour ses équipements automobiles extérieurs, galeries, porte vélos, coffres de toit, etc, Thule est un groupe suédois, sis à Malmö, employant environ 2500 personnes de par le monde. Créé en 1942, il n’est venu au business de la chaîne qu’en 2004, en rachetant Koenig. En dépit de son nom allemand, la marque est 100 % italienne, produisant à Molteno depuis 1966. Et depuis 2014, date du rachat par Thule, elle reste seule en piste pour König, toujours liée aux professionnels, et Thule qui reprend une partie du catalogue König pour les ventes à des particuliers qui connaissaient déjà bien la marque à travers ses réputés coffres de toit. En 2014 rien n’a changé, avec seulement quelques fabrications spéciales en Pologne, l’usine américaine de Seymour étant à 100 % consacrée aux produits « outdoor » and bags ». Les chaînes ne représentent que 15 à 20 % du CA global de 400 millions d’euros mais la fourchette des pourcentages ne peut être plus précise car dépendant beaucoup de la météo. Selon ses caprices, la demande peut monter en flèche, ce qui pose d’énormes problèmes à l’unique usine de fabrication des chaînes, Molteno : « En cas d’hiver rigoureux, nous pouvons être amenés à doubler notre production. Cela nous est arrivé en 2012 avec un record à 1 million de chaînes » explique Alberto Guidotti, Managing Director de Thule SpA. Il a organisé l’usine autour d’une idée simple, la souplesse. Elle doit être capable, quasiment en une journée de doubler sa production, d’où des installations qui peuvent paraître surdimensionnées en temps normal mais qui sont « justes » en cas de forte demande. Dans ces circonstances, l’intérim devient obligatoire, les 150 personnes habituellement employées à Molteno peuvent en récupérer une centaine supplémentaire pour une troisième équipe et surtout doubler les flux au montage, avec un maximum théorique de 1,3 million de chaînes. Cette adaptabilité est aussi indispensable à la rentabilité d’une entreprise qui débute tôt sa production en mars (sur les bases d’une année moyenne), mais seulement les ventes en novembre, mais qui doit aussi « digérer » les stocks de de l’année précédente en cas de mévente... Autant dire que gérer Molteno demande une sacrée boule de cristal, que semble posséder Alberto Guidotti, ancien de Pirelli câbles, qui a fait de Thule SpA une affaire rentable. Comme il s’occupe aussi du marketing et de la R&D, 100 % à Molteno, on peut le féliciter du succès de cette très innovante Easy-fit.
Qualité d’abord
Deux leaders, chacun avec 20 % des ventes, tirent le marché mondial, Thule et l’Allemand Pewag. Les 60 % restant sont de plus en plus dominés par les produits à bas prix venant d’extrême-Orient. En France, Thule s’attribue 30 à 35 % d’un marché français toujours variable en fonction du temps, estimé de 200.000 à 300.000 chaînes par an. Cette excellente position doit beaucoup à sa filiale française, située en Savoie et animée par Sylvain Lallemant, un spécialiste hyper pointu très écouté à Molteno, apport d’autant plus stratégique que la France s’inscrit comme le second marché de Thule, derrière l’Italie et devant l’Allemagne. Cette réussite qui perdure, on la doit évidemment à la qualité globale du produit. Alberto Guidotti développe le concept : « La qualité du produit est primordiale, mais elle ne serait rien sans celles de la conception, du process, du design mais aussi de tout ce qui concerne le client, avec le montage en priorité ». Et pour montrer combien l’usine de Molteno est « verte », elle affiche à son entrée un tableau lumineux indiquant combien elle économise d’électricité grâce aux panneaux photo-voltaïques recouvrant ses toitures. Elle est aussi exemplaire pour l’eau et les rejets divers, elle est qualifiée ISO 9001 et 14001 depuis des années, avec la nouvelle 18001 en cours. La visite du bureau d’études rassure sur les contrôles à tous les niveaux et ouvre les yeux sur des problèmes jamais évoqués. Ainsi Thule n’achète que des aciers de grande qualité (26 grades différents!), de première fusion, bien meilleurs mais plus chers que ceux incorporant des ferrailles de récupération. Test décisif, la rupture d’un maillon n’est obtenue qu’après une énorme traction de plus de 5 tonnes : sportivement, les ingénieurs de Thule signalent qu’ils sont à égalité avec leur rivaux de Pewag et Weissenfels, bien au dessus de la norme et des chaînes bas de gamme - bas prix. Autre grosse différence avec ces concurrents low cost, la taille des maillons, souvent trop allongés pour économiser du métal.
Enfin, cette « analyse concurrence » vous ouvre les yeux sur certaines tromperies de concurrents (pourtant réputés), plus difficiles à détecter, comme le diamètre réel des fermetures des cerclages intérieurs, largement au dessus de celles annoncées. Ainsi on a pu constater de visu qu’une chaîne annoncée à 9 mm en faisait 10 à 12 en certains endroits de la fermeture du cerclage. D’où risque de friction sur des pièces de sécurité (freinage) pouvant devenir graves. Cet aspect peu connu des chaînes pouvant frotter sur les organes de suspension ou de freinage devient de plus en plus préoccupant avec les voitures récentes. L’espace sous les passages de roues y est de plus en plus compté, d’où les précautions des constructeurs qui bottent en touche en annonçant ces voitures « non chaînables ». Comme on ne peut priver ces modèles de traction sur la neige, les ingénieurs de Thule ont mis au point des dispositifs uniquement fixés sur l’extérieur de la roue, comme le Thule K-Summit, à peine plus long que la Easy-fit à monter sur les boulons de fixation de la roue, grâce à la très pratique clé fournie. Autrement dit, l’appellation « non chaînable » ne doit plus faire peur, elle impose simplement un autre type de matériel.
Process parfait
Depuis bientôt 50 ans Thule fabrique des chaînes de qualité, montrant un process à la fois techniquement parfait et rentable. L’opération de base consiste à fabriquer des chênes en continu, de différents diamètres de fil pour obtenir à l’arrivée les fameux 7 mm, 9, 12 ou 16 mm de hauteur qui caractériseront le produit fini. Des petites machines transforment d’abord en continu le fil d’acier préalablement décapé en lui donnant une section semi circulaire : la partie ronde formera l’intérieur du maillon, qui pourra ainsi facilement pivoter par rapport au suivant. Le fil tronçonné est coupé puis replié pour constituer un maillon, lequel pivote de 90° tandis que le maillon suivant est fabriqué. La soudure intervient après, le courant électrique chauffant au rouge est deux parties touchantes du fil, qui fusionnent. Le premier contrôle qualité intervient tout de suite après, une forte traction s’assurant de la qualité de la soudure : qu’elle lâche et toute la mini chaîne s’arrête...
Reste à durcir la surface des maillons qui auront à frotter sur la chaussée et devront résister à l’abrasion. Thule dispose pour cela d’un énorme four, où les chaînes « recuisent » jusqu’à 6 heures à 900° avant d’être plongées dans l’eau. Essentielle pour la qualité, cette trempe durcit l’extérieur pour mieux résister à l’usure. La couche doit être épaisse, mais pas trop pour laisser le cTmur du métal plus souple et moins cassant, cette séquence est suivie et validée en continu par le bureau technique. Et pour donner un bel aspect argenté aux chaînes, celles-ci sont plongées dans des bains de galvanisation. La couche de zinc n’intervient pratiquement pas dans la résistance de la chaîne mais les clients apprécieraient peu des chaînes noirâtres...
Vient alors l’assemblage final de la chaîne complète (cerclages, verrouillages, barrettes, échelles, etc), forcément manuel : çà et là de grandes tables métalliques semblent attendre des ouvriers. « Notre usine est rentable telle quelle, pour une production calée sur des valeurs annuelles moyennes, mais il faut prévoir les possibles pics de la demande. Le montage est équipé pour recevoir le personnel intérimaire dont nous avons besoin en plus des 40 postes permanents. Certes il faut le former mais nous avons la chance de pouvoir compter sur des gens qui l’ont été lors des années précédentes », assure Alberto Guidotti. Plus loin, pour les lourdes et complexes chaînes PL et GC, Thule a installé des robots ABB. Un investissement élevé rendu indispensable dès lors que le temps de montage devient très important : « A Molteno, le coût de l’heure travaillée revient à 40€, à 8€ en Pologne. Voilà le pourquoi des robots ici et des petites séries spéciales que nous fabriquons en Pologne ». Quant à la dernière étape, l’emballage des chaînes, elle mobilise tout autant Thule. La qualité du design, l’ergonomie des boîtes ou sacs, la facile compréhension des notices de montage, les accessoires comme les gants, tout est étudié dans les moindres détails et rentre de plain pied dans la démarche qualité de Thule.
Easy-fit vraiment facilement
On savait depuis Equip Auto 2011 l’extrême facilité de montage de la chaîne Easy-fit. Mais après les travaux pratiques (obligatoires!) de Molteno, on ne peut qu’être une nouvelle fois ébloui. Après un premier essai à environ 30 secondes, le second ne dépasse pas effectivement les 12 secondes. Il suffît pour cela de bien coincer le haut de la chaîne sous le menton, bien écarter les bras, les mains tenant fermement les parties rouges du cerclage intérieur. Sans mollir, correctement agenouillé sur la large sacoche de l’Easy-fit, il suffît de « jeter » la partie supérieure de la chaîne sur le sommet du pneu puis de placer le reste sur la face extérieure de la roue. Il ne reste plus qu’a mettre le tout en tension en appuyant – avec le pied mais la main suffît pour les costauds – sur le cliquet repliable glissant sur la barre d’aluminium. C’est fait. La voiture avançant, en avant ou en arrière, de quelques dizaines de centimètres et toute la chaîne se verrouille à la seconde même. Le démontage est tout aussi facile, instantané grâce à des verrous en plastique rouge, visibles, ergonomiques et intuitifs. C’est à l’évidence le meilleur système de montage des chaînes, et l’on ne voit vraiment pas comment on pourrait faire mieux... C’est si vrai qu’un des projets de Thule consiste à conserver ce principe pour les VU. En attendant, cette merveille est déclinée dans une grand nombre de dimensions et de largeurs, CU-9, CU-10, et pour équiper de façon efficace les gros SUV en Easy-fit SUV.
Mais pour offrir un panel complet et pas seulement une chaîne parfaite et haut de gamme, Thule a conçu les CS-9 et CS-10 à tension et démontage automatique, les CG-9, CG-10, CL-10 et XG-12 pro à tension automatique. Moins chère car basiques avec leur tension manuelle, les CD-9, XD-16, CB-12 et XB-16 nécessitent deux arrêts, d’abord pour le montage, le second pour ajuster la tension. Toutes ces références sont assez faciles à décrypter, les chiffres terminaux 9, 10, 12, 16, indiquant le diamètre de la chaîne, les plus petits pour les véhicules légers, les plus gros pour les SUV et utilitaires.
Dernier test révélateur, monter une chaîne K-Summit pour véhicule « ayant un encombrement de roue réduit », autrement dit non chaînable. Une fois la chaîne positionnée, une clé Thule – gainée de caoutchouc pour éviter la gêne du métal froid – permet de la fixer solidement a partir d’un écrou de roue. C’est plus long mais sans problème particulier, cette K-Summit est bien pratique et disponible en plusieurs largeurs pour s’accommoder de nombreux véhicules, berlines en version standard, XL pour SUV et Crossovers, XXL pour leurs versions supérieures à 2 tonnes. Et comme toutes les chaînes Thule, ces produits sont homologués pour l’Europe et les pays imposant des normes (Autriche, Suisse, Italie, etc) et surtout garantis 5 ans. Après visite de Molteno on se dit que Thule pourrait sans doute aller bien au delà ! A suivre dans le prochain numéro : La chaîne prouve et chiffre sa supériorité.