Tivoli, l’âme de Yokohama Trelleborg Wheel Systems
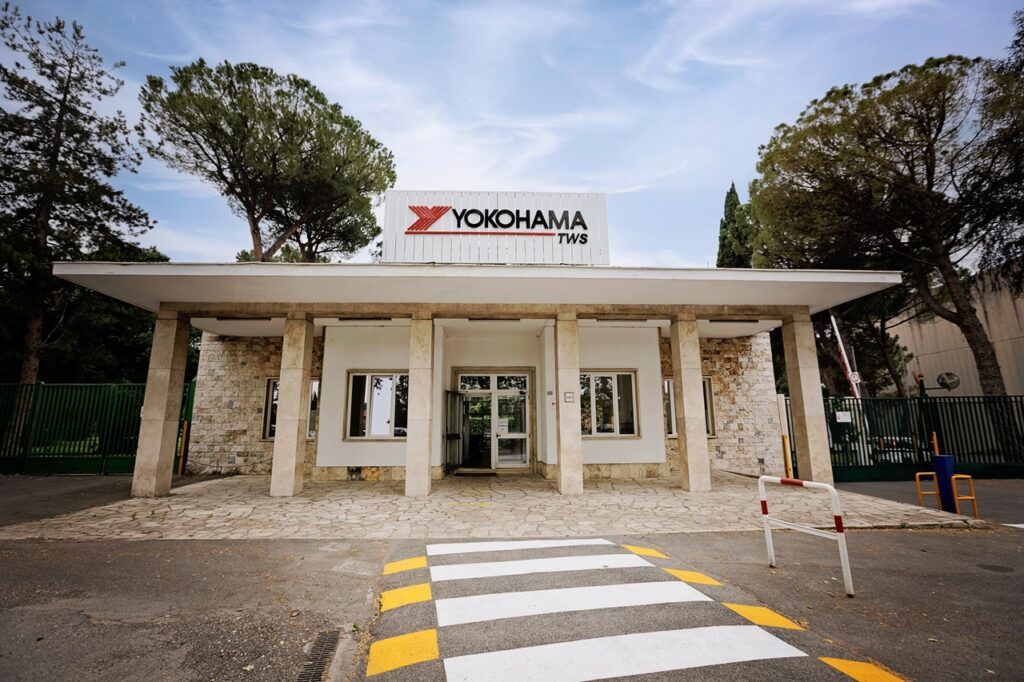
C'est un endroit totalement atypique. Presque hors du temps. Située à une vingtaine de kilomètres à l’est de Rome (Italie), la ville de Tivoli a bâti depuis plusieurs siècles son équilibre économique sur quatre piliers. Les oliviers, la vigne, le travertin (roche calcaire) et le pneumatique sont ainsi inscrits dans son histoire. Si le caractère terrien de cette cité du Latium lui colle parfaitement à la peau, son visage industriel, lui, s’immisce dans les rues riches de bâtiments en pierres taillées, marquées par la douceur du quotidien.
Preuve que le contenu et le contenant s’épousent à merveille, l’usine locale de Yokohama Trelleborg Wheel Systems s’incorpore parfaitement dans cet environnement. Passée la porte d’entrée, on découvre alors un site où les bâtiments se fondent dans ce cadre verdoyant. Un héritage du passé. Car le lien entre Tivoli et le pneumatique a commencé à se tisser en 1930.
Cette année-là, Pirelli inaugure une usine dans le quartier Villa Adriana. Celle-ci sera pendant cinq décennies le principal employeur de la ville, rassemblant à son apogée jusqu’à 700 personnes. Dans les années 1980, face à une demande déclinante, Tivoli perd en attractivité et son activité décline progressivement. En 1999, Pirelli cède ce site à Trelleborg qui souhaite en faire son cœur industriel et y implanter son siège social européen.
Agile par nature
L’outil est redéfini pour assumer les spécialités du suédois que sont l’agricole, la construction et la manutention. En parallèle, une guest house, implantée sur une parcelle attenante et nichée au milieu d’oliviers vieux de plus de 200 ans (dont la production profite aujourd’hui aux 380 salariés), est réhabilitée. C’est de là que Paolo Pompei, PDG du manufacturier (pour encore quelques mois avant de rejoindre Nokian Tyres), et ses équipes pilotent le rayonnement mondial de Trelleborg Wheel Systems.
Toujours en parfaite autonomie, malgré le rachat de la firme par Yokohama en 2022, comme le détaillait récemment dans nos colonnes le dirigeant. Depuis 25 ans, la place de Tivoli dans l’écosystème Trelleborg est toujours restée cruciale. Au fil du temps et des développements, l’usine a perdu son titre honorifique de plus grand site du groupe, étant aujourd’hui reléguée derrière ses homologues tchèque et sri-lankais.
Mais en rassemblant à la fois des lignes de fabrication, un centre de recherches et développements ainsi qu’un autre de tests et de validations, l’implantation italienne additionne les talents ainsi que les atouts. Elle demeure aussi un modèle d’agilité et d’adaptabilité permanentes, eu égard à ses spécialités. Car savoir développer et produire des enveloppes allant de 10 (manutention) à 30 pouces (agricole) demande forcément ce genre de qualités.
Sur le plan industriel, l’agricole pèse ici un poids considérable compte tenu de ce que représente celui-ci dans l’activité globale de YTWS. Sur un total de 1,2 milliard de chiffre d’affaires annuel, la part des pneumatiques destinés aux professionnels de la terre et des cultures s’élève ainsi à 75 %.
Une production semi-automatisée
À Tivoli, environ 500 enveloppes agricoles sortent quotidiennement des chaînes. Pour faciliter le processus de production, la totalité des composants est fabriquée en interne, tandis que l’assemblage est réalisé in situ, sur un poste de travail unique et semi-automatisé. Une partie des volumes, pour les plus grandes références, bénéficie en effet de robots.
Ces derniers se chargent notamment de la cruciale étape de la pose de la bande de roulement sur la carcasse devant un opérateur qui n’a plus à s’abîmer la santé avec des tâches fatigantes. Évolution notable dans le procédé de fabrication maison, cette même bande n’est plus en une seule et unique pièce, mais en plusieurs morceaux dont la pose est définie au micromillimètre près par les machines.
La cuisson est quant à elle assurée par l’une des 62 presses présentes dans l’usine, de tailles très hétérogènes avec des produits qui peuvent varier de 250 à 500 kg. Le processus peut aller de 1h30 à 2h30, avec 24 bars de pression et une cuisson s’élevant à 200 degrés. Une fois cette étape terminée, une phase de refroidissement est nécessaire.
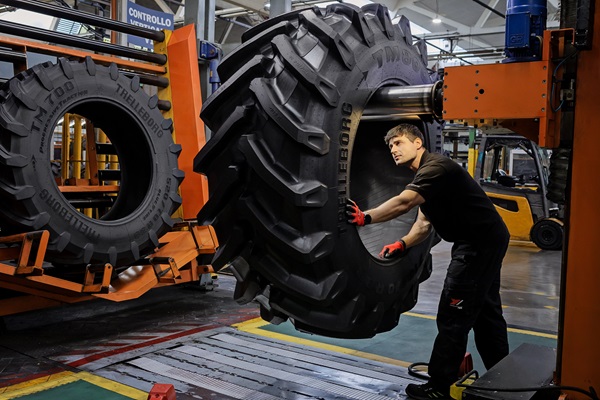
Environ 500 enveloppes agricoles sortent quotidiennement des chaînes de production de l’usine italienne. ©Yokohama
Celle-ci va demander entre 30 et 40 minutes pendant lesquelles l’enveloppe va rester à l’horizontale. Une obligation pour éviter la moindre déformation. Après quoi, l’ensemble de la production fait l’objet d’un contrôle visuel par un opérateur spécialisé, avant que le pneumatique rejoigne le magasin de stockage situé un peu loin dans l’enceinte italienne.
Toujours dans une logique de simplification et d’optimisation, tous les déplacements intermédiaires des enveloppes, d’un poste à un autre, sont automatisés grâce à l’aide de robots autonomes. En définitive, si le site fait son âge dès qu’on lève les yeux, tout le processus de fabrication dénote par son niveau de technicité et de modernité.
Des outils de tests particulièrement sophistiqués
Une impression confirmée dans un autre bâtiment situé non loin de là. Le travail d’essais revêt à Tivoli une importance majeure. Comme c’est le cas en République tchèque, en Chine, au Brésil, au Sri Lanka et dans le nord de l’Italie, YTWS dispose près de Rome d’une infrastructure de tests hyperperfectionnée avec de multiples outils à disposition.
Un premier permet de contrôler l’usure et la profondeur des nouveaux produits. Un autre analyse la performance de ces derniers, que ce soit en termes d’adhérence, de durabilité ou encore de résistance au roulement selon des cycles de vitesse allant de 70 à 100 km/h. À quelques mètres de là, un caisson hyperbare permet quant à lui de réaliser des tests de pression en appliquant 2,5 fois celle recommandée la réglementation européenne.
Enfin, signe de l’évolution des technologies, un dernier espace est consacré à l’analyse de la longévité des batteries des capteurs. Une phase importante dans tout le cycle de R&D alors que les solutions connectées tendent à se généraliser. Une belle manière de faire le lien entre le passé et le futur.
Car la grande force de ce site, par la volonté de Trelleborg depuis 25 ans, est d’avoir su évoluer en saisissant les opportunités de croissance qui s’offraient à lui. Et cette philosophie n’est pas près de changer. Le virage de l’électrification des motorisations et le défi des pneus verts (voir encadré) devraient considérablement amplifier le caractère de pointe de Tivoli. Entre les oliviers, les innovations vont encore fuser.
ENCADRE
Le 100 % durable espéré pour 2035
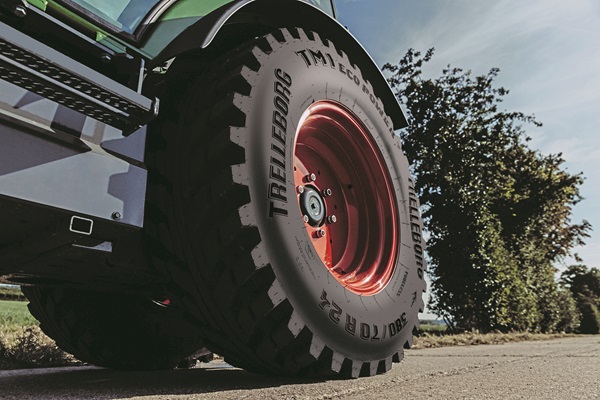
Commercialisé depuis début 2024, le TM1 Eco Power comprend 65 % de matériaux renouvelables, recyclés ou biosourcés dans sa composition. ©Yokohama
Principal site de production du groupe en Europe avec la manufacture tchèque, l’usine de Tivoli de Yokohama Trelleborg Wheel Systems n’a pas seulement pour ambition de faire du mass market. Derrière ses murs, c’est aussi l’avenir du manufacturier qui se joue, avec notamment l’équipe de recherches et développements européenne. Comme tous ses confrères, YTWS s’est lancé dans une incroyable quête. Incroyable, car très ambitieuse et terriblement complexe.
"Réussir à produire des pneumatiques plus respectueux de l’environnement est un défi pour notre industrie dans son ensemble. Nous voulons contribuer à sauvegarder la planète. Le travail de nos ingénieurs est incroyable, car ils voient loin et raisonnent large", expliquait récemment dans nos colonnes le PDG de la firme, Paolo Pompei. L’objectif de créer un pneumatique 100 % durable est partagé par les principaux acteurs de cette industrie. Tous s’attachent à s’en approcher progressivement.
Du vert et du local
YTWS revendique d’avoir à date des produits comprenant 65 % de matériaux renouvelables, recyclés ou biosourcés. C’est notamment le cas du TM1 Eco Power qui constitue une belle illustration de ces efforts. Développé pour les tracteurs électriques, ce pneu est commercialisé depuis début 2024 en quatre dimensions, alors que de nouvelles sont attendues dans les prochains mois. Preuve de ses atouts, le TM1 Eco Power a été choisi en première monte par le constructeur Fendt.
Le 100 % durable, lui, est attendu pour 2035 et se double d’un autre défi. "Nous voulons aussi le relever en créant une économie locale vertueuse, précise encore le dirigeant. Il faut réussir à utiliser des fournisseurs locaux plutôt que d’autres provenant du bout du monde." Polymère, noir de carbone, hévéa, huiles… Tous ces composants peuvent provenir du monde entier et centraliser, ou rapprocher tout au plus, leur production des sites d’assemblage demeure crucial. Le manufacturier y travaille sans relâche et Tivoli prend une part active dans cette orientation.
Cet article est extrait du Journal du Pneumatique n°187 de novembre-décembre 2024.